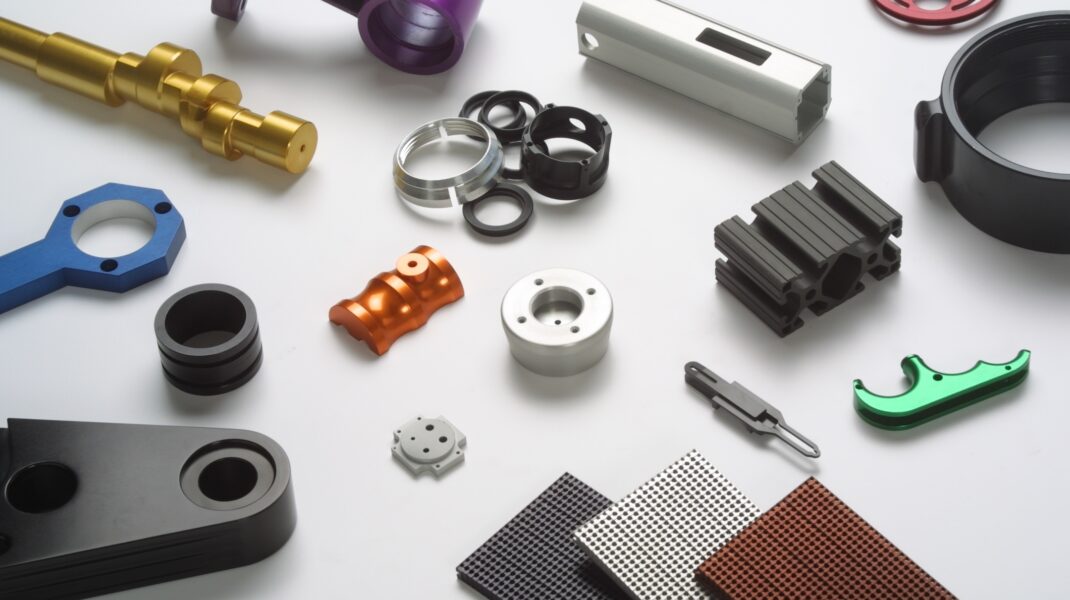
How Alloy Selection Influences Our Aluminum Finishing Processes
It’s no surprise that material selection establishes a final part’s properties from its strength and durability to its electrical conductivity. Different applications call for different materials, which require specific finishing techniques to achieve the optimal outcome.
Our services don’t just rely on whether a customer sends us clean aluminum parts with an even surface finish. We must consider the precise alloy when determining what finishing methods will produce the intended end product.
Let’s walk through the different finishing processes for aluminum, as well as some unique considerations based on particular alloys. As always, don’t hesitate to contact us regarding any specific questions you may have.
Aluminum Metal Finishing
In its raw form, aluminum is a fragile, easily damaged material. When exposed to the elements, it forms an oxide layer that naturally protects it from corrosion. Our finishing processes build upon that oxide layer for added durability and protection. These services include:
By the time we’ve completed our processes, the material’s strength is second to a diamond!
Alloy Distinctions
Not all aluminum alloys are the same. Each has its own unique properties that may impact necessary finishing processes and/or the finished outcome. A few examples of this include:
- We do not hardcoat 2024 aluminum. The copper content in this aluminum alloy is so high that it begins to burn during hardcoat.
- 5052 is generally a coarser alloy due to higher magnesium levels. Magnesium dissolves in the anodize tank, making the surface slightly rougher.
- 7075 aluminum is typically more yellow than other alloys. Hardcoat ranges from yellow to gray. There’s more color variation with 7075 than 6061 due to alloying elements.
Aluminum Testing Solutions
To verify that all components have the necessary protective coating, corrosion resistance, abrasion resistance, and coating weight, our team facilitates several tests for coating analysis. Global Metal Finishing has both the internal capability and external contacts necessary for testing, not to mention our NADCAP accreditation for chemical processing and AS9100 certification, which solidifies our auditing processes.
Top-Notch Metal Finishing Services
No matter what aluminum alloys appear in your blueprint, Global Metal Finishing is the right vendor to take on your finishing operations. Here are some highlights of working with us:
Manufacturing Design Consulting
When OEMs have questions during the component design process, they can connect with our team to develop blueprints. Based on the part’s unique requirements, as well as the specific alloys being used, we can offer advice to ensure optimal finished parts.
Intricate Masking Abilities
Our masking department performs one of our standout services at Global Metal Finishing. We mask per customer specifications to protect critical areas from coating.
Additionally, we perform dual processes in which we mask one area and perform one service – such as chemical conversion – then mask that portion before conducting another process – like anodizing. These dual services are more time-consuming than our traditional metal finishing methods, but they are invaluable for components with multiple surface finish requirements and areas.
Process Expertise
Some of the machine shops we work with know exactly what finishing processes must be performed on their components. Others know what the finished parts should look like but aren’t certain what techniques would accomplish this. Our team prides itself on understanding what our customers need even before they do. Based on the precise alloy and machining processes utilized, we think critically about what metal finishing services suit your project.
Whether or not you know what information to include when requesting a quote, you can trust Global Metal Finishing to provide exceptional customer service and deliver parts on time and in spec.
Leave a comment
You must be logged in to post a comment.